Issues & Splitting Method
Is it worth recycling compressors? Absolutely yes. Scrap compressors contain lots of copper and can be found everywhere in our lives, in numerous electronics such as air conditioners, refrigerators, and other refrigeration equipment. A typical air conditioner compressor contains about one to two kilograms of copper. The copper content in an ordinary compressor can vary from ten to over thirty pounds, depending on factors such as the manufacturer, model, and size. However, although people are aware of this, they remain skeptical about the compressor recycling business. This hesitation arises from the potential pitfalls that they might encounter initially. This article aims to outline common mistakes in compressor splitting and provide guidance on how to avoid them.
Inappropriate Preparation and Compressor Type
Your potential failure for optimal AC compressor recycling may exist in the following incorrect preparation.
●Failure to Drain Refrigerants: Failing to properly drain refrigerants from the compressor can release harmful chemicals into the environment. Refrigerants are potent greenhouse gases that contribute to global warming.
●Incomplete Removal of Oil: AC compressors contain lubricating oil, which needs to be thoroughly drained and recycled. Inadequate removal of oil can contaminate the recycling process, increasing the complexity of recycling.
Besides, most people wonder: Is buying waste compressors for recycling a money-losing business? Definitely no, but it can be if you have purchased the wrong types. Copper compressors and aluminum compressors are common types in the market. As we all know the price of copper is higher than aluminum. Thus, purchasing copper compressors for recycling tends to yield greater profits.
However, the challenge lies in how to identify whether the purchased compressor is made of copper?
Distinguishing between copper compressors and aluminum compressors without cutting the outer shell can be done in three ways.
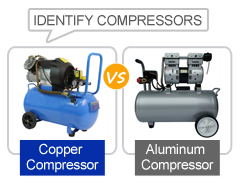
●First, if the upper cover is in a circular shape and has no pit, then it is a copper one; otherwise, it’s vice versa.
●Second, check out the refrigerant that this compressor uses. If it uses any of these(134a/R12/R22), it must be a copper compressor.
●Industrial appliance compressors should be copper-type.
●Check the nameplate of the compressors. The aluminum compressor has one more “L” than the copper compressor on the nameplate.
Issue of Manual Splitting
Hand dismantling has been proven to be a cost-effective choice for recycling compressors. However, the method contains too many potential hazards, both in terms of safety and copper loss. The method is easy to fall into the following pitfall. By avoiding these mistakes, you can ensure a safer and more efficient process when working with scrap AC compressors.
●Lack of Proper Tools:
Scrap compressors, being waste motors encased in hard metal shells, are a challenge for removal. Splitting a waste compressor lacks appropriate handhold tools. This makes the process unsafe and imprecise, leading to a further reduction in potential profits.

●Forceful Disassembly:
Manual dismantling without experienced workers may turn compressor dismantling into an unprofitable venture, as the force applied for splitting is difficult to control. Excessive force can damage the copper wire coils within the compressors and make it challenging to separate components correctly. Such damages exacerbate the financial losses and inefficiencies experienced in the compressor recycling business.
●Lack of Safety Precautions:
Using handheld tools to separate compressors exposes workers to dangerous situations, especially when neglecting to wear appropriate safety gear such as gloves and safety glasses. Manually dismantling can lead to injuries from sharp edges, electric sparks, or harmful substances. Dismantling waste for extra money is nice, but it’s not worth the effort if you accidentally get hurt.
Overall, manual dismantling itself has such as being labor-intensive, time-consuming, dangerous and incompatible with larger-scale recycling tasks. So it is imperative to use more advanced and automated techniques to solve these limitations, ensuring a safer, more efficient, and environmentally friendly recycling approach.
What’s the Best Way to Split AC Compressor?
The AC compressor splitting machine is equipped with essential components like a hydraulic system, rotary disk mechanism, lifter and four cutting blades. The lifter handles the up-and-down movement of the compressor, while the high-speed rotary disk enables the cutting blades to precisely and rapidly slice through the compressor’s outer casing. This setup ensures efficient and accurate compressor shell cutting.
In total, there are need 3 steps to splitting a compressor:
1: With compressor shell cutting machine to cut case first;
2: Take out the inner stators,
3: Choose a proper motor wrecker machine to recycle compressor stators.
As technology advances, the large volume of global electronic waste renders manual dismantling impractical. Therefore, more advanced automatic electric compressor recycling machines prevail. These machines reduce labor and cost investments, simplify the working procedure, eliminate the need for special training, and compensate for any errors that manual handling might introduce. Automatic recycling offers improved efficiency, accuracy, and safety by swiftly disassembling compressors, separating valuable components and recycling them with minimal waste. It’s evident that using a compressor recycling machine is the best way to prevent the compressor splitting mistakes mentioned before.
Leading Manufacturer 3T
3T provides both compressor shell cutting machines and compressor stator cutting and pulling machines overseas. Our machines adopt hydraulic cutting technology equipped with high-precision claws for automatic processing. They can split a compressor shell in 30-60 seconds with precise markings, ensuring no damage to any of the inner components. The stator recycling machine ensures the complete removal of copper windings without any loss. Besides, we offer BSC electric motor recycling machines for dismantling both ordinary motors and compressor motor stators.
3T ensures industry-standard machines through rigorous testing.
Confused about machine investment? Struggling with purchase decisions? Buying a machine is crucial. 3T covers comprehensive service and assurance. Our support is ongoing even post-purchase. No one-size-fits-all, we respect individual needs. Contact us: 008613772508206 for customized.
Compressor Splitting Business Is Worthwhile
Whether the compressor splitting business is worthwhile is a challenging question to answer due to several influencing factors. If you make any of the mistakes I mentioned earlier or you buy faked motors it could result in a loss of business;
1: Buy scrap motors at the right price.
2: Choose the right machine.
However, investing in a compressor recycling machine allows you to process more scrap compressors, maximizing your profits. To acquire a waste compressor recycling machine, you can reach out to 3T products page. Company for top-quality equipment. We hold the patent for the compressor recycling machine and guarantee to optimize your recycling revenue. If you have any inquiries, please don’t hesitate to contact us.